- 僕は3Dプリンタが欲しくてたまりません。最近はまっている電子工作の部品を自分の思い通りに作りたいと思ったからです。でも高くてすぐに買える値段ではありません。お母さんが、「データが自由自在に作れるようになって活用できるところをアピールできれば買ってあげるかもしれない」と言いました。そんな夏休み、データの作り方を学ぶためにGooDay Fab Daimyoでワークショップに参加し、そこでFAB 3D コンテストを知りました。このために作品を作ることで僕の欲しい3Dプリンタのすごさを伝えることができる!それに入賞すれば(夢のような話だけど…)3Dプリンタがもらえるって!?まさにチャンス到来です。
- 今年の夏は暑すぎ、暑すぎ、暑すぎる!毎年涼しくなるために行く好きなプールにも、行きたくなくなるほどの暑さです。僕の大事なノートパソコンも熱を持ちすぎてぷしゅんと悲しい音をさせて落ちてします。それで持ち運びに便利なサイズの携帯型扇風機を作りたい、そしてそれを僕の研究テーマにしたいと思いました。いつもでもどこでも風を浴びられれば、僕もパソコンもハッピーになるはず。3Dプリンタは使えるし好きな工作もできるし出来上がったら扇風機として使えるし嬉しいことだらけ!
ハンドクーラー ~携帯型扇風機~

Owner & Collaborators
License
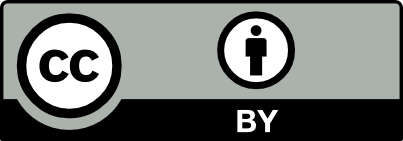
Summary
「ハンドクーラー」は、僕オリジナルの電池式(単三電池2本)で動作する携帯型の扇風機です。
今年の夏はじめて使いかたを習った3Dプリンタを使って試行錯誤しながら作りました。
ハンドクーラーを作った経緯からでき上がるまでの過程と難しかった点や工夫した点をまとめました。
今年の夏はじめて使いかたを習った3Dプリンタを使って試行錯誤しながら作りました。
ハンドクーラーを作った経緯からでき上がるまでの過程と難しかった点や工夫した点をまとめました。

Materials
Tools
Blueprints
Making
- FAB 3Dコンテストに応募しようと決心したその日すぐにパーツを揃えました。電子部品はいつもネットで買ってもらいますが、すぐに欲しかったのでどこに売ってるかお父さんに聞いてヨドバシカメラに行って買いました。電池ボックスは、本体にどのようにセットするかを考えて出し入れのできるものを選びました。スイッチも色々検討しましたがトグルスイッチが一番カッコイイと思いました。本体(ケース)はもちろん3Dプリンタで作成します。
- パーツを簡単に組み立てて動作することを確認しました。そして、これらがちゃんと入るように本体の大きさを考えました。
- 電気パーツの大きさから本体の大きさ、スイッチの出てくる穴の位置を調整しました。ファンは、3Dデータの素材の公開されたサイトからとってくればいいとアドバイスをもらいましたが、どうしても自分で作ったものを動かしてみたいと思ったので、自分で作ってみました。
- 自分のパソコンで作ったデータを、3Dプリンタ出力させるためにUSBドライブで移動して専用ソフトで開きます。画像はファンと筒のふた(上下2つ)を開いたところです。
- 僕が設計したファン、まるでスクリューみたいでした!実際にモーターをつなげて動くかどうかを確認しました。いい具合に回転はするけど、なぜか前に風がこない!?後ろに風が来ていました。ファンの回転方向を逆向きにすることで解決しました。
- 問題が発生しました。サイズを測っていたはずのモーターが入りません。ふたも明らかに閉まりません。どうやら設計ミスです。やり直します。
- 太くなって持ちにくくなるかなとも思いました。先生にもそう言われましたが、それでも大きい方がカッコイイという僕の考えで、太いまま出力してみることにしました。
- いざ、再出力!の前に、何度も失敗はできないのでよくよく確認します。実際にモーターの3Dデータを作成してTinkerCAD上で組み合わせてみたらいいよという先生のアドバイスをもとにやってみたら、モーターの先端が穴から3mm程度しか出ないことが判明!先端にも3Dプリンターで接続用パーツを作ることにしました。
- 先にモーター接続用パーツを3Dプリントしてみました。なかなかいい感じに刺さっています。
- 【印刷時間(再出力)】・ふた(2つ)… 約1時間半・本体となる筒 … 約6時間前回の出力した感じから、もう少しあらく出力してもよさそうだなと思ったので調整して時間を短縮しました。また、前回サポートがペンチとニッパーで頑張ってもなかなかとれなくて傷だらけで困ったので、今回は素材を以前使ったことのあるABSに変えてもらいました。取れやすくなりました。
- 左:ビフォー 右:アフターなんということでしょうだいぶ太くなりました。
- サポートがこんなにたくさん取れました!もったいないような…僕はひらめきました。フィラメントは3Dプリンタの中で溶かしてから形が作られているんだから、3Dプリンタにこの不要になったサポートをまとめて入れる所を作って、これをまた溶かして再利用できたらいい!大人になったら商品化するぞ!と思ったら、もうそういったものが作られているということを後で聞いて知りました。やっぱり皆同じことを考えるのですね。
- 出来上がったパーツに仕組みを取り付けていきます。
- 再度仕組みを装着。熱収縮チューブ、とてもいい感じです。
- ついに完成しました!ファンがよく回っています。電源ON/OFFランプの豆電球も光っています。自分でイメージしたものが実際に形になりこうやって動かせると本当に嬉しい気持ちになります。
- 今回はここまでで完成としましたが、今後も工夫して使いやすいように改造したいと思っています。
- 再出力時に太くなるのはわかっていましたが、実際に実物大に出来上がってみると思った以上に太くなりすぎて持ちにくくなってしまいました。持ちやすいように持ち手を作るとか細い部分を作るなど形を考えなおしたいです。
- 今回はファンを自分で作ろうと思い自分の思うイメージだけでデータを作成しましたが、もっといろいろな扇風機の形を確認するなどファンの形を研究して、もっと風がよく出るようなファンの形状にしたいです。また、スクリューのように太く重くなったので薄型にもしたいなと思います。
- 先生からアドバイスを受けてファンの種類についてネットで調べてみました。
- プロペラファン -> 今回使った形のもので風量が多いファン
- シロッコファン -> 換気扇などに使われるプロペラファンよりも強力でブロワーなどにも使われる
- クロスフロー -> 室外機に使われプロペラファンよりも弱い
- プロペラファン -> 今回使った形のもので風量が多いファン
- 実は最初のアイデアでは光センサを組み込んで明るい時にファンが回るようにしたいと考えていました。光センサの回路を勉強して組み込もうと頑張ったのですが、サイズ的に組み込むことができず今回は断念しました。次回つくるときはこれも組み込めるようにしたいです。画像は、CdSセル(光センサー)とArduino(マイコンボード)で周囲の明るさを判定して、LEDの点灯を制御するプログラムをテストしている様子です。他にも、距離センサを使って顔や手などを近づけたときに回すような仕組みを作るのもいいなと考えました。
- 今回PLAとABSの二つを出力してベースやサポートの取れやすさが変わりました。他にどのような素材があるのか、どのような違いがあるのか、フィラメントの種類を調べてみることにしました。【フィラメントの種類】約12種類あるそうです。【主要なフィラメント】
- ABS -> 一般的なプラスチック製品で広く使われている素材。
- PLA -> 対応している3Dプリンターの多い素材。
- PC(ポリカーボネイト) -> プラスチック素材の中では最高レベルの耐衝撃性。軽くて丈夫、iPhone5のボディ。
- 上記が3Dプリンタで使われるメインの素材とのことですが、以下のような素材もあるそうです。【その他フィラメント素材】
- PET(ポリエチレン・テレフタレート) -> 透明性があり、強度、耐久性、耐熱性に優れている ペットボトルの素材に使われている。 3Dプリンターは積層して造形するため、そのぶん透明度が低くなる。
- PETG -> PETの強化版。PET以上に高い透明性があり、強度、耐久性、耐熱性に優れる。化粧品の容器など高機能なボトルに使われる。
- PET(ポリエチレン・テレフタレート) -> 透明性があり、強度、耐久性、耐熱性に優れている ペットボトルの素材に使われている。 3Dプリンターは積層して造形するため、そのぶん透明度が低くなる。
- 僕はPETGの素材をネットで見てとても気に入りました。きれいな形のオブジェとか作ると良さそう!いつかこの素材を使って作品を作ってみたいなと思いました。
References
Usages
Project comments

Comments