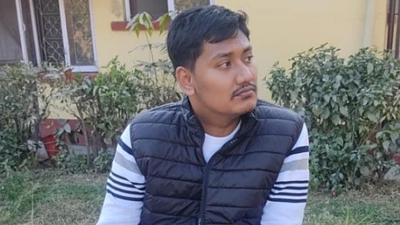
- He sustained a C5 spinal cord injury due to a fall, resulting in quadriparesis (partial paralysis in all four limbs). He has limited fine motor control, low triceps strength, and poor body balance, making it difficult to perform daily tasks. He requires assistive support to enhance independence.
- Cause: Sustained a C5 spinal cord injury from a fall off a small cliff in Shivapuri during a hike
- Challenges:
- Limited function in all four limbs
- Requires support for daily activities
- Low triceps strength and poor body balance
- Goal: To achieve independence in daily life and perform tasks on his own
Comments